Quality control measures are essential to ensure consistent and reliable plastic spiral coil binding results. Here are some key measures to consider:
1.Equipment Maintenance:
Regular equipment maintenance is critical to ensure the smooth operation of binding machines.
Conduct routine inspections to identify wear and tear on punch dies, cutters, and coil insertion tools.
Implement a maintenance schedule that includes cleaning, lubrication, and replacement of worn parts to minimize downtime and prevent binding errors.
2.Document Preparation:
Before binding, meticulously inspect documents to be bound.
Trim excess edges to achieve clean, uniform edges for a polished appearance.
Verify that all pages are properly aligned to prevent misalignment issues during binding.
3.Coil Inspection:
Inspect plastic spiral coils for deformities or imperfections that could affect the binding process.
Maintain a record of coil batch numbers and sources to trace and address quality issues if they arise.
4.Pitch and Hole Alignment:
Ensure precise alignment between the document's hole pattern and the coil's pitch.
Utilize alignment aids, such as templates or guides, to maintain consistency in hole placement.
5.Proper Coil Sizing:
Select the appropriate coil size by considering the document's thickness.
Accurate sizing prevents over-tightening or insufficient binding, guaranteeing document integrity.
6.Tight Coil Insertion:
Utilize coil inserters with adjustable speed settings to control the coil's insertion rate.
Properly guide the coil through the holes, ensuring it passes smoothly through each page.
7.Coil Crimping:
Utilize a dedicated crimping tool to secure both ends of the coil.
Apply consistent pressure during crimping to prevent coil unwinding or misalignment.
8.Sample Binding:
Conduct sample bindings at the beginning, middle, and end of production runs.
Evaluate these samples for alignment, tightness, and overall quality, making adjustments as necessary.
9.Operator Training:
Ensure that binding operators receive comprehensive training on the equipment's operation and maintenance.
Regularly update training materials to incorporate best practices and safety guidelines.
10.Quality Assurance Checks:
Implement a quality control team or process to oversee binding operations.
Randomly inspect bound documents, documenting any deviations from quality standards.
Establish clear criteria for acceptable quality and deviations that warrant correction.
11.Document Thickness Consideration:
Adhere to the manufacturer's guidelines for the maximum document thickness that can be bound with plastic spiral coils.
Regularly review these guidelines to stay informed of any updates or changes.
12.Document Orientation:
Ensure that all pages within a document are oriented correctly before binding.
Correct any misaligned pages to avoid readability issues and maintain a professional appearance.
13.Customer Feedback:
Encourage customers to provide feedback on the quality of bound documents.
Use this feedback to identify areas for improvement and address any customer concerns promptly.
14.Documentation:
Maintain thorough records of quality control checks, equipment maintenance, and any issues encountered during the binding process.
These records serve as a valuable resource for troubleshooting and process improvement.
15.Continuous Improvement:
Regularly review and assess the binding process with the goal of enhancing quality control measures.
Implement changes, upgrades, or procedural improvements based on data and feedback to maintain consistent and reliable binding results.
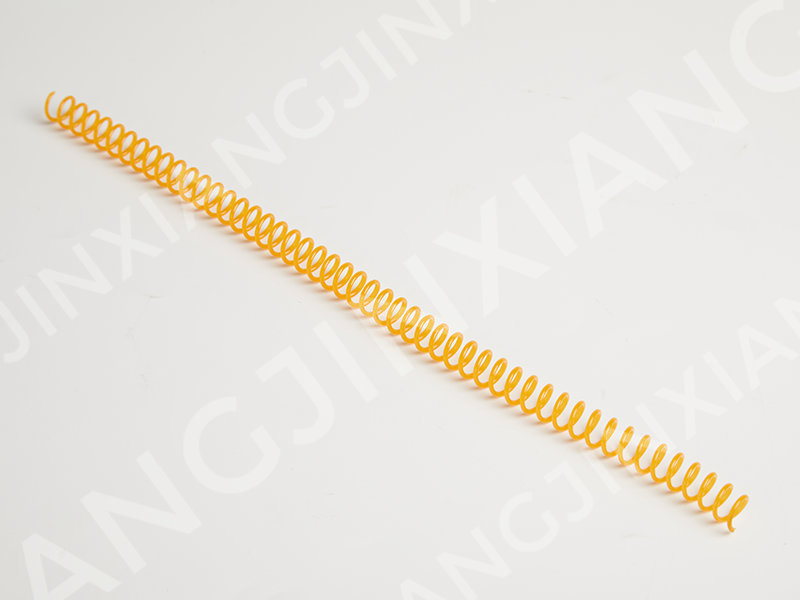
Multi-color optional, regular 48rings, can also be customized.
PACKING: White corrugated box/ Color box.